When the General Motors stamping plant in Kalamazoo, Michigan, shut its doors in 1995, few could imagine any kind of bright future for the massive site it left behind. For decades, the plant had been a key source of stable employment, producing vital automotive components behind its towering walls. Within its sprawling, 2.2-million-square-foot building, thousands of skilled men and women once worked shifts that kept the place humming day and night. The plant’s closure suddenly left 4,000 workers without jobs. It dealt a painful blow to the local economy, which had grown to depend on GM’s steady presence. The constant sound of metal stamping and machinery was replaced by an unsettling silence. Many in the community wondered what would become of this empty giant, and how long it would stand as a grim reminder of lost prosperity.
But not everyone saw a dead end. Some looked at the property’s 340 acres along the I-94 corridor and saw the potential for something else—something that could breathe new life into a wounded region. One of these forward-thinkers was Hackman Capital Partners (HCP), an entrepreneurial real estate investment and operating company that believed it could reshape the abandoned plant into something far more dynamic.
Rather than allowing the old facility to languish as a rusting relic, HCP envisioned a vibrant multi-tenant business park, equipped with cutting-edge features, adaptable zoning, and infrastructure primed for a shifting economic landscape. HCP purchased the property from General Motors in 1999 and is the owner/developer. Midlink President, Rob Britigan, who represents HCP explained, “Essentially, HCP anticipated a need before there was a demand. Despite the challenges of the redevelopment, we knew we could transform the property in a way that would be good for business and industry—and good for Kalamazoo.”
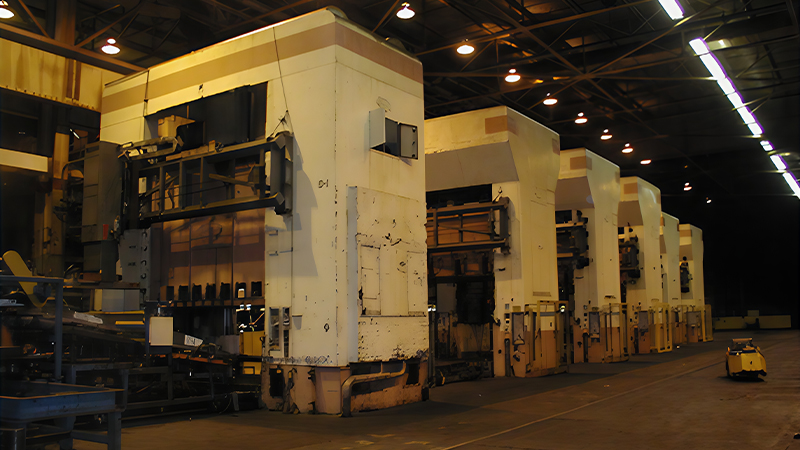
Before its transformation into Midlink Business Park, the former General Motors stamping plant in Kalamazoo stood silent, with its vast factory floor and towering stamping equipment serving as a stark reminder of the thousands of jobs lost when the plant closed in 1995.
The Bold Transformation Begins
At first glance, this vision might have seemed overly optimistic. After all, the building’s entire design revolved around a single function: manufacturing essential automotive components. It was never intended to host a wide range of tenants or to handle the logistics demands of modern supply chains. But HCP saw its potential. The property’s sheer size, its prime location right off a key transportation corridor, and its existing utility infrastructure were all valuable starting points. To bring tenants in, though, the old plant would need much more than a simple facelift. It would have to be rethought and re-engineered in a significant way.
The first step was a bold redesign of the structure itself. Originally, the plant was a huge, single-purpose building that did not suit multiple tenants. That had to change.
“The property was not practical or logistics friendly as a multi-tenant hub,” Rob recalled. “So we literally split the building in two, by removing more than 300,000 square feet and creating a 1,200’ x 240’ truck plaza between the two new buildings that could accommodate up to 110 truck docks.”
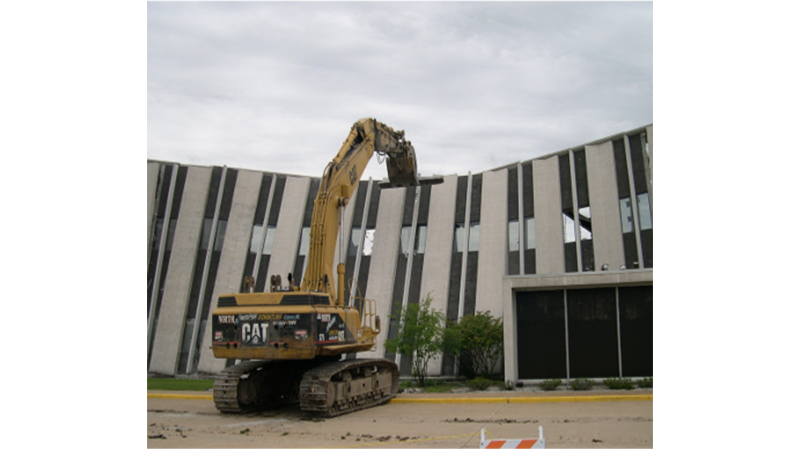
During the early stages of redevelopment, crews removed portions of the old GM stamping plant to reconfigure the space, making way for Midlink Business Park’s modern, multi-tenant design.
This drastic move opened up the interior space, making it possible for different tenants to operate side by side with easy access for deliveries, shipping, and distribution. Instead of one big, sealed box, the property now had a central logistics hub designed to handle a wide range of trucking operations. With the new configuration, businesses of various sizes and industries would find it easier to move products in and out, a crucial factor for any modern tenant.
Yet splitting the building was only one part of the transformation.
“In addition to renovating the building, we created more than two miles of public and private roads, four traffic entrances and reworked the rail system to provide easy access to the site and open the surplus land for development while preserving 38 acres of wetlands,” said Rob.
Infrastructure improvements were essential. With multiple roads and improved rail access, the park could connect quickly to regional and national markets. Preserving the wetlands was another key point, showing a commitment to environmental responsibility even while investing heavily in redevelopment.
Beyond the major structural changes, the developers took numerous steps to make the space more appealing to companies. They introduced a new façade, modern flooring, better lighting, and office spaces that did not feel like part of an old factory. They installed new signage and added attractive storefront-like tenant entryways.
“We also reworked the utilities and made dramatic exterior and interior renovations—a new façade, new tenant storefront-like entryways, new signage, flooring, painting, lighting, and offices—that not only increased functionality, but also created a modern, new appearance,” Rob explained.
The goal was to ensure that when potential tenants toured the place, they would see opportunity, not a remnant of the past.
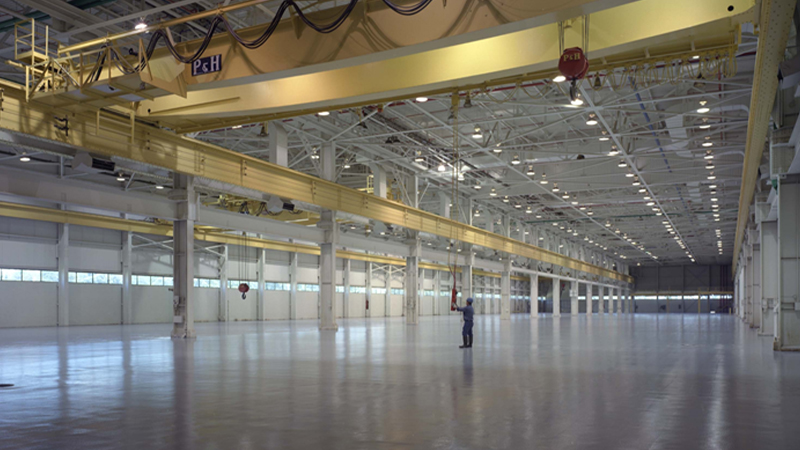
Inside the revitalized facility: the once aging GM plant now boasts a clean, modern, and expansive interior, ready to accommodate diverse businesses and industries under one roof.
Collaboration and Economic Revival
But no matter how well-designed the facilities were, tenants would not magically appear without incentives and a supportive business environment. Early on, HCP and its team recognized they needed to work with local and state authorities to make the property as inviting as possible.
“Our strategy was to rebrand the property, collaborate with the local and state authorities to establish flexible mixed-use zoning and attain business incentives, such as a tax-free Renaissance Zone, and then promote Midlink with aggressive target marketing,” said Rob.
Flexible mixed-use zoning meant businesses from different sectors—manufacturing, logistics, office, retail—could settle in without dealing with restrictive land-use rules. The tax-free Renaissance Zone allowed tenants to operate in a more cost-effective way, especially important for companies weighing where to invest and grow.
The collaboration did not stop at zoning and tax incentives. Southwest Michigan First (SMF) became an important partner for the evolving business park.
“We created a symbiotic relationship,” Rob said. “SMF was established in 1999 as a private economic development organization with a motto of ‘the greatest force for change is a job,’ and we were building a place that would create jobs and prosperity. As a regional economic development leader, SMF worked with Midlink to facilitate development and, as it still does today, help attract businesses to the Park. SMF, along with other public partners, helped us weave ourselves into the fabric of the community.”
This relationship connected Midlink to a broader network of businesses, gave it credibility, and helped integrate it into the larger regional economy. Over time, Southwest Michigan First played a part in attracting prospective tenants, highlighting the park’s advantages and helping to close deals.
Within a few years, the project began to show tangible results. Jobs started coming back to the area. Diverse companies moved in, taking advantage of the upgraded infrastructure and incentives. One early milestone was securing the first tenant in 2004. This proved to everyone that the concept was not just a dream—the park could indeed host successful businesses.
“Closing the transaction with GECC in 1999; removing the 156 stamping presses from the building, plus 700 tons of scrap steel, 300 truckloads of wood block and 200 tons of dust and debris; completing redevelopment efforts, and moving our first tenant into Midlink in 2004,” Rob listed as significant achievements.
Over time, the park reached stabilized occupancy, proving that the demand was real and that the initial gamble had paid off.
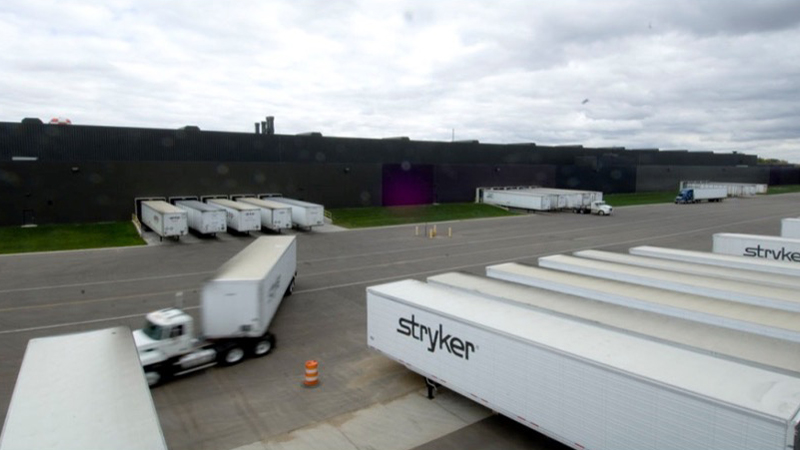
The newly constructed 1,200-foot truck plaza, designed with 110 loading docks, allows for efficient logistics and streamlined operations—transforming Midlink Business Park into a vital hub for modern supply chains.
A Future of Opportunity and Resilience
As the park grew, it began attracting an impressive mix of tenants, including Kaiser Aluminum, W. Soule, Mann & Hummel, and Landscape Forms. Companies like Behler-Young Company, an HVAC/R distributor, and AIT Worldwide Logistics, specializing in retail and e-commerce logistics, found tailored spaces at Midlink. Additionally, major names such as General Mills, Concordance Healthcare Solutions, Airway Oxygen, Schupan & Sons, Hark Orchids, Marriott, and Zeigler Motorsports highlighted the park’s broad cross-industry appeal. By catering to such a wide range of sectors, Midlink strengthened the local economy and provided resilience against industry-specific downturns.
This diversity also helped rebuild the community’s job market. With about 1,500 jobs created and around 2,000 individuals interacting on-site daily, Midlink helped restore economic vitality that had been lost when GM left. If one sector faces a downturn, others can remain stable. This approach creates a buffer against the kind of shock that hit Kalamazoo in 1995. Ultimately, it helps maintain a vibrant, healthy community.
“Midlink has contributed by building value, creating a significant number of jobs, and driving investment into the local community,” Rob noted. “Midlink has also given philanthropically by supporting various non-profit organizations in the area, hosting networking events, and participating in various business and community initiatives.”
Another key advantage of Midlink is that it offers a blueprint for other communities facing similar industrial closures. Throughout the United States, old factories and vacant industrial sites sit idle, reminding locals of better times and prompting difficult questions about the future. The transformation at Midlink shows that with vision, cooperation, and a willingness to take risks, these properties can be turned into modern economic engines.
“Create a clear vision, assemble the right team, think strategically, develop relationships, and collaborate for success,” Rob advised to young entrepreneurs and economic developers who might be facing their own challenges elsewhere.
Looking back over 25 years, the difference is striking. What was once a quiet, empty, and somewhat depressing landmark—an abandoned GM plant with nothing but memories of lost jobs—has become a bustling, multi-tenant hub of activity. Tenants build their own success stories there, creating good jobs, providing needed services, and investing in the local economy. HCPs early belief in the site’s potential proved correct.
“The vision for the next 25 years is to continue creating value by developing the remaining surplus land with retail and industrial buildings,” Rob said.
These ambitions underscore that Midlink’s story is far from over. With land still to be developed and opportunities on the horizon, the project stands as a testament to adaptability and forward thinking. As the economy evolves, so too will Midlink, building on its past successes while shaping a future of continued growth and innovation.